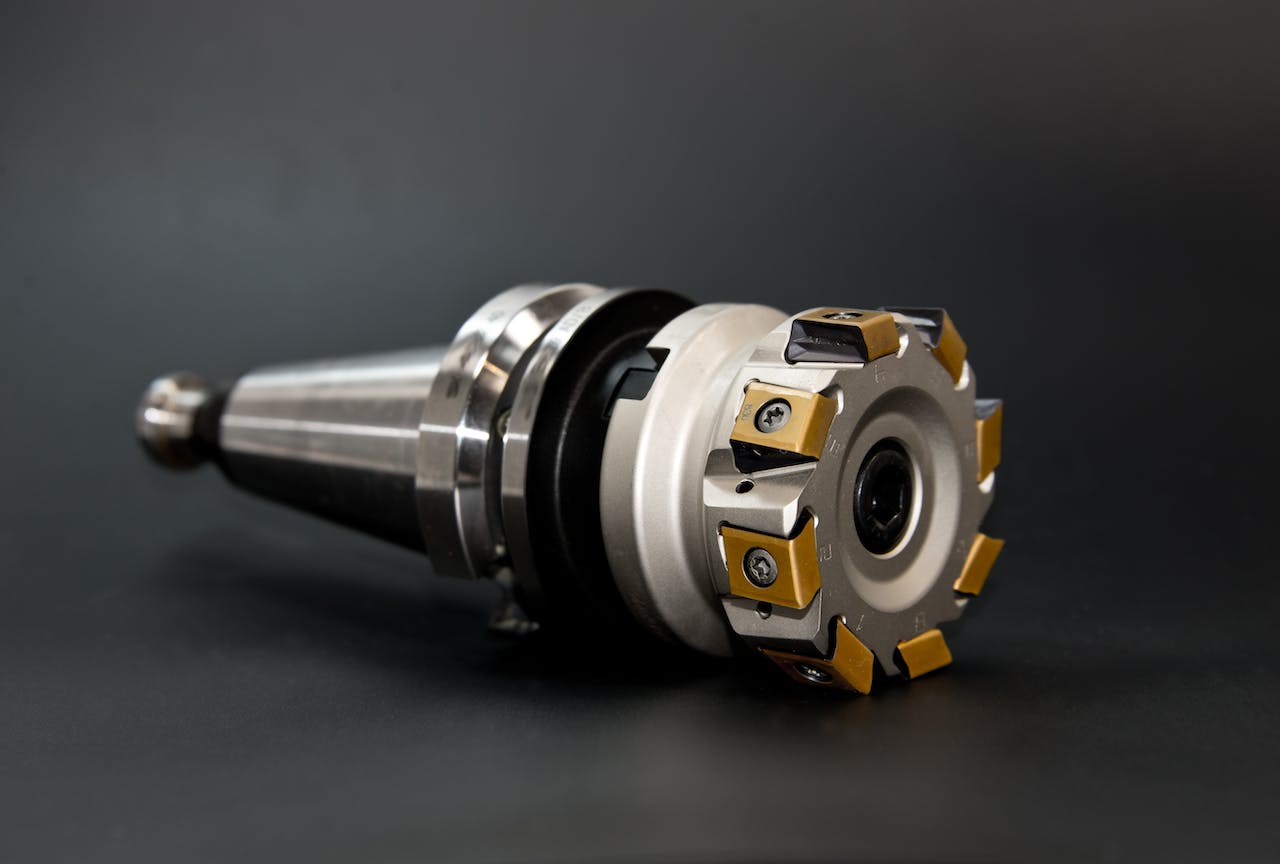
Not all manufacturing segments used CNC machining as often as they do now. A long time ago, the production process was controlled by manually operated machinery. Machining operations were labor-intensive since these machines usually only needed one operator, who was frequently a professional machinist, for each milling machine, lathe, and grinder.
Long-running procedures occasionally permitted a clever worker to figure out how to run many machines, but this was uncommon. Machine shops eventually saw automation for the first time with the introduction of the numerical control (NC) machining technique.
Machining instructions were punched onto paper tape, which was then read by a tape reading device. NC programs could not be stored, were hard to change, and were only sometimes dependable. Every time, a fresh tape had to be made.
By incorporating computerized controls, computer numerical control (CNC) developed from and enhanced the numerical control technique. This article will examine the many types of CNC equipment, their functions, their use by manufacturers, and what buyers should consider. But first, to help you appreciate these fantastic machine tools, here is some background knowledge.
What Is CNC?
A CNC machine, short for Computer Numerical Control machine, is a computer-controlled device used in manufacturing processes. Its main objective is to fabricate or alter different components and items made of materials like plastic, wood, metal, and more. This technology revolutionizes manufacturing because it offers accuracy and automation.
A drive or motion system, a feedback system, and a command function are the three main parts of a CNC machine. The drive system manages the machine's physical movement, and the feedback system's real-time data guarantees precision. Digital instructions produced by CAD (Computer-Aided Design) and CAM (Computer-Aided Manufacturing) software are interpreted by the command function.
One of the main benefits of CNC machines is their capacity to automate industrial processes, which, when compared to manual techniques, results in faster output and greater accuracy. CNC machines are essential instruments in contemporary production, with applications ranging from metallurgy and carpentry to aerospace and automotive.
What Is The Function Of CNC?
Controlling the movements of a machine tool is the fundamental purpose of computer numerical control (CNC). Control, automation, and monitoring of the movements of CNC tools are all accomplished through the collaborative efforts of digitized data, a computer, and a computer-aided manufacturing (CAM) application.
Smaller hobbyist versions often make use of an external computer, as opposed to larger industrial machines' standard practice of employing an integrated computer as a dedicated onboard controller.
Each CNC controller collaborates with a number of motors and drive components in order to carry out and regulate the motions that have been programmed. On more complex machines, there is a feedback system that continuously analyzes and changes the speed of the cutter as well as the feed rate and location of the cutter.
Essential Elements Of CNC Machine System
The following is a list of components or pieces that are typically discovered in a CNC machine system.
- Disk drives, specialized information devices, keyboards, computers, and other types of hardware all fall under the category of information input/output devices.
- Internet connection, which may also include Ethernet, HSSB (High-speed data transmission port), Processing LAN, RS 232C interface, and other networking options.
- Control unit for external mechanical shafts, such as those found on an exchange bench, an unloading and loading robot, and the driving shaft of a tool magazine
- Providing input to the servo drive and motor unit
- Motor and drive unit for the spindle
- The numerical control component is known as the CNC control unit.
- Controller of the PMC
- Unit of the machine that is responsible for feedback and position measurement
- The input and output units for the control signal are located on the power cabinet of the machine.
Type Of Software Commonly Used In The CNC Machining Process
Computer Aided Drawing (CAD)
The majority of CNC initiatives begin with the installation of CAD software. There is a wide variety of CAD software available, but all are utilized in the process of design creation. AutoCAD, SolidWorks, and Rhino3D are some of the most well-known CAD systems. There are also cloud-based CAD solutions, some of which offer CAM capabilities or interact with CAM software better than others. Some of these cloud-based CAD systems offer both.
Computer Aided Manufacturing (CAM)
CAM software is frequently responsible for the creation of the programs that CNC machines utilize. Before the machine conducts any actual cutting, the user is able to run cutting simulations, select tool paths, and coordinate workflow by creating a "job tree" with CAM. CAM systems are frequently implemented as add-ons to CAD software.
Their primary function is to create a g-code, which directs the CNC tools and workpiece moving components in the appropriate direction. The use of CAM software's wizards makes programming a CNC machine far more straightforward than ever before.
Mastercam, Edgecam, OneCNC, HSMWorks, and Solidcam are some of the most well-known names in CAM software. According to a survey from 2015, Mastercam and Edgecam together account for approximately half of the market share for high-end CAM software.
Different Types Of CNC Equipment
CNC Equipment, a cutting-edge technological marvel, has revolutionized industries worldwide. CNC Equipment, often referred to as Computer Numerical Control Equipment, is a vital component of modern manufacturing processes. With CNC Equipment, precision and efficiency are paramount.
This robust CNC Equipment allows for intricate and precise machining, enabling manufacturers to meet the highest standards of quality. As we delve deeper into the realm of CNC Equipment, we'll uncover its diverse applications across various sectors. From CNC Equipment for metalworking to CNC Equipment for woodworking, this versatile technology is indispensable.
CNC Router Machines
A computer numerical controller (CNC) is a professional automatic machine tool that uses a tracking system to direct the X, Y, and Z axes to move and uses G-code commands to direct the router bit to cut along the path of the tool produced by the CAD/CAM programs and eliminates the excess parts on the substrate to achieve the final results of eliminating texts and designs. A CNC router is also known as a computer numerically controlled router.
Depending on the needs of the company, CNC router kits may be compatible with a variety of controllers, including DSP, Mach3, Mach4, NcStudio, LNC, OSAI, LinuxCNC, PlanetCNC, Syntec, Siemens, and FANUC, among others. CNC routers can do relief carving, rotary carving, flatbed cutting, and 3D routing on a variety of materials, including wood, aluminum, copper, brass, glass, plastic, acrylic, and foam.
Lathe CNC Machine
The material of the workpiece is rotated about a primary axis when the CNC lathe machine is operating. This is how the machine works. Cutting tools on a lathe removes material from the workpiece and shapes it according to the requirements of the project.
Swiss machining, drilling, knurling, turning, and sanding are some of the many processes that are well-suited for CNC lathe machines. Other applications include turning. The CNC machines that fall under this category find use in the manufacturing of things like furniture, barrels for firearms and baseball bats, camshafts and crankshafts, musical instruments, and more.
However, because of the method by which this machine produces items, it is preferable to generate symmetrical components.
Drilling CNC Machine
One standard piece of equipment in CNC machine shops is the Drilling CNC Machine, which is especially useful for hole-drilling activities. Its primary purpose is to make holes in different kinds of materials with specialized cutting instruments called drills or drill bits. These holes fulfill many functions, such as taking screws, satisfying aesthetic specifications, or making it easier to do secondary assembly procedures.
Drilling CNC machines are used in many different sectors, including woodworking, engineering machinery, mold making, astronautics, automotive manufacturing, and shipbuilding. They are vital in these industries because of their accuracy and adaptability.
The Drilling CNC Machine's limited capacity to drill holes with enormous size or considerable depth without the use of specialty drill bits is one of its drawbacks, though. Notwithstanding this drawback, these devices nonetheless have a significant impact on production, helping to create accurate and dependable holes in a variety of materials for a range of industrial uses.
CNC Plasma Cutter
Cutting a material using a plasma torch is what the term "plasma cutting" means, which describes the procedure. This technique is most frequently utilized while cutting through robust materials like steel and several other types of metal.
A CNC plasma cutter works by forcing gas through a nozzle at a very high rate of speed. During this process, an electrical arc occurs between the surface being cut and the gas that is emerging from the nozzle. The gas is being used to cut the surface.
Some of the gas is turned into plasma as a result of this process, and the temperatures of the plasma range from 10,000 to 50,000 degrees. The plasma has a temperature that is high enough to melt the material that is being cut, and it also can blast away any molten metal that may be present at the location of the cut.
CNC plasma cutters are somewhat comparable to CNC routers in terms of their dimensions and general appearance. These devices are only capable of working with flat forms.
CNC Electric Discharge Machine
An instrument for precise metalworking and forming conductive materials is an electric discharge machine (EDM) CNC. Because EDM uses electrical discharges instead of typical cutting procedures, it may be used to create complicated and detailed designs that are difficult to accomplish using traditional methods.
An electrode, usually composed of graphite or copper, and a workpiece make up a CNC EDM machine. Utilizing deionized water as a joint dielectric fluid, a conductor is employed to link the electrode and workpiece. Sparks or discharges produced by an electric current flowing through the electrode erode the material from the workpiece in a highly regulated way.
CNC EDM machines can create complex patterns and incredibly tiny details with great precision because of this technology. They are frequently employed in sectors like aerospace, mold and die manufacture, medical device manufacturing, and mold making.
Hardened steel and exotic alloys are among the materials that CNC EDM machines are particularly good at cutting and shaping. Their proficiency in attaining precise measurements and complex patterns renders them vital in contemporary production procedures where accuracy and excellence are critical factors.
Waterjet Cutting CNC Machine
This piece of machinery uses a narrow stream of water to slice through various materials. Because it is able to make clean cuts through virtually any material, CNC water jet cutting is one of the most versatile cutting methods.
The material that a waterjet cutting machine can cut includes rubber, leather, fiberglass, diapers, circuit boards, foam, paper, porcelain, glass, stone, and sheet metal. This makes the waterjet cutting machine highly flexible.
The waterjet cutting speed is significantly lower in comparison to the cutting speeds of other available options. This is one of the most significant drawbacks. This reduced pace is particularly noticeable at the curving cuts and curves of the course.
CNC 3D Printer
Using a process known as additive manufacturing, a CNC 3D printer is a type of equipment that creates three-dimensional items by reading digital data and printing them out. During this procedure, material is deposited one layer at a time in order to construct the finished product.
The adaptability of 3D printing and the capacity to produce intricate geometries are both advantages of the technology; nevertheless, it does have certain limitations. Since the initial investment in CNC 3D printing equipment can be expensive, and the printing process itself could be more efficient, this method is not ideal for large-scale mass manufacturing.
Despite this, it has been put to use in a wide variety of fields, such as prototyping, custom manufacturing, aerospace, healthcare, and education, where its capacity to make detailed and individualized components has proven to be quite helpful.
8 Things To Consider Before You Buy CNC Equipment
Purchasing CNC (Computer Numerical Control) equipment might be an extensive choice for companies trying to improve their production efficiency. CNC machines provide automation, accuracy, and adaptability to a wide range of industries, including woodworking, healthcare, and the automobile and aerospace sectors. But before you spend this money, there are a few essential things to think about to make sure you get the best CNC machine for your requirements.
Purpose And Application
Determine the primary function and planned uses of your CNC machine first. Various CNC machine types are tailored to do specific jobs, including laser cutting, 3D printing, milling, and turning. The kind of CNC machine that best meets your demands will depend on how well you understand your production requirements. To reduce your alternatives, take into account elements like manufacturing volume, part complexity, and material compatibility.
Quantity And Size Of Machine
Important factors to take into account are the CNC machine's capability and physical dimensions. Make sure the machine can handle the dimensions of the parts or components you plan to produce.
Take into account your facility's space constraints, weight capacity, and maximum workpiece dimensions. Your production process may become limited and inefficient due to undersized or oversized machinery.
Machine Configuration
There are several different types of CNC machines, including multi-axis machines, horizontal machining centers (HMCs), and vertical machining centers (VMCs). The arrangement you choose will rely on the kind of job you intend to perform.
While HMCs are often utilized for more significant, more complicated components, VMCs are appropriate for operations like drilling, milling, and contouring. For complex tasks, multi-axis machines provide more precision and versatility. Determine which configuration best suits the machining needs you have in mind.
Workholding And Tooling
Think about the possibilities for work holding and tooling that are compatible with the CNC machine. The cutting tools, drills, and inserts needed for machining processes are included in the tooling.
Please make sure the machine can effectively change and manage tools throughout production and that it supports the tooling you require. Work-holding fixtures are necessary to clamp and place the workpiece firmly during machining. To maximize your production setup, assess the machine's compatibility with several work-holding options.
Precision And Tolerance
In CNC machining, accuracy is essential, and the degree of precision you need will depend on your application. Take into account your items' tolerances and surface polish requirements.
Select a CNC machine that can reliably fulfill your quality standards, as different models provide differing degrees of precision. To keep consistent outcomes over time, it's also critical to take the machine's repeatability and stability into account.
Control System And Software
The software and control system of the CNC machine are essential to its functionality and usability. Make sure the software and control interface match the programming requirements and experience of your team by evaluating their capabilities. A few features to look for are the ability to import CAD (Computer-Aided Design) files, G-code compatibility, and conversational programming. Take into account the manufacturer's technical support and software upgrades as well.
Budget And Total Cost Of Ownership
Establish a budget for the CNC machine's initial purchase as well as its long-term ownership. The machine itself, tools, software, and any required extras are all included in the original purchase. But it's also critical to take into account recurring costs like energy use, operator training, and maintenance. To make an educated financial choice, figure out the machine's total cost of ownership (TCO) throughout its anticipated lifespan.
Supplier And Support
Select a trustworthy CNC machine provider who has a reputation for producing high-quality goods and providing top-notch customer service. Check the manufacturer's reputation online, peruse client testimonials, and get recommendations.
Ask about warranty coverage, spare part availability, and technical support services' response as well. A trustworthy provider can significantly impact the performance of the machine and your whole CNC machine ownership experience.
CNC Machine Manufacturers In The USA
Tormach and Carbide 3D are two US-based makers of reasonably priced CNC machines. A variety of CNC equipment, such as milling machines and lathes, are available from Tormach, and they are renowned for being reasonably priced without sacrificing accuracy or quality. They serve small companies as well as enthusiasts, opening up CNC technology to a larger market.
Conversely, Carbide 3D specializes in desktop CNC machines, especially those from the Nomad and Shapeoko series. These little machines are ideal for makers, innovators, and small workshops since they are made with a budget in mind.
For those wishing to get into CNC machining without going over budget, Tormach and Carbide 3D provide affordable solutions that still yield dependable and competent equipment for a range of uses.
CNC Equipment - FAQs
What Is The Purpose Of A CNC Machine?
To assist in the creation of cutting-edge and inventive items, a CNC machine may be used to scan, clone, engineer, and reverse-engineer components.
Why CNC Is Better?
The CNC machine's precision guarantees a constant level of product quality.
Is Using A CNC Simple?
Although learning the CNC machining process might be difficult, it is definitely not impossible.
Conclusion
CNC equipment unmatched accuracy, automation, and adaptability have completely changed modern production. Electric discharge machines, 3D printers, lathes, and milling machines are just a few examples of how CNC technology has revolutionized several sectors. Businesses can now increase output, cut down on mistakes, and quickly build complex components thanks to it.
However, choosing the best CNC equipment necessitates giving serious thought to a number of aspects, including budget, size, configuration, precision, and purpose. Making an informed choice guarantees that CNC machines support long-term success in addition to meeting urgent industrial demands. CNC equipment stays at the cutting edge of innovation as technology develops, promoting quality and efficiency in the industrial industry.